High-Quality Switchgear Equipment – With Integrated Designs
EPLAN Cogineer and Pro Panel at Siemens
At its facility in Leipzig, Germany, Siemens designs and builds type-tested low-voltage power distribution boards and motor control centres for the SIVACON S8 production series. The standardisation achieved with EPLAN Cogineer saves the Siemens electrical engineers a lot of time, while simultaneously improving quality – as does the three-dimensional control cabinet design made with EPLAN Pro Panel, which the company implemented at the same time. As a next step, Siemens is also planning to add cloud-based EPLAN services to intensify and simplify cooperation among its international manufacturing facilities.
Siemens has developed a low-voltage power distribution system and motor control centre – the SIVACON S8 – that is being used in many of the company’s international infrastructure projects. Typical applications include energy distribution in data centres and other infrastructure projects, but especially motor control centres in power plants and in the oil, gas and process industries. The variety of applications and specifications is correspondingly large.
The lead factory for designing and manufacturing this system is located in Leipzig, Germany, and is part of the Smart Infrastructure Distribution Systems business division. Michel Strusch, Head of Electrical Engineering in Leipzig and overall Project Manager for the company’s “Wiring 4.0” project, explains: “Our contract partners are mostly part of the Siemens Group, but the majority of deliveries go to external customers.” Nearly eighty per cent of the manufactured systems are installed outside of Germany.
Mass Customisation for Control Cabinet Design and Manufacturing
The switchgear systems being built in Leipzig mainly have between 5 and 25 panels with widths from 400 to 1200 millimetres. But projects with more than one thousand panels have also been realised. Usually these are fully customised, one-off systems. As Strusch explains: “Every project has its own special – and very demanding – requirements, the degree of repetition is quite low and the variance increases with every new project.”
This makes standardisation for these projects even more important for Siemens. That’s why the design engineers in Leipzig developed a configurator for the SIVACON S8 years ago. It considerably simplifies and accelerates project planning because the project engineers can rely on type-tested functional modules for their work. However, this standardisation initially only applied to the main circuits, meaning the energy circuits. The main task for the electrical engineers was thus to design the secondary circuits and control circuits.
The Goal: Standardising the Secondary Circuits As Well
The next step was to expand the standardisation to these electrical circuits as well. Technical Coordinator Benjamin Herold was responsible for the project: “We’ve been working with EPLAN in electrical engineering since 2008.” Therefore it made sense to use EPLAN Platform also to automate schematic creation.
For this they took a systematic approach. Working with an EPLAN consultant, in 2017 they worked out the basics for automated schematic creation using EPLAN Cogineer. As Herold explains: “We first deconstructed the individual functions and components in the control circuits down to the lowest level. Then we structured and combined these components so that they formed units that could be used in the best possible manner.”
Automatic Schematic Creation
The design engineers thus created a solid and very practical foundation for designing the control circuits. Herold: “EPLAN Cogineer is intuitive to use. The electrical design engineer selects the devices and/or functions and the schematic largely creates itself.”
This saves time but also offers additional advantages – for instance, Siemens was able to achieve a stronger degree of standardisation. Strusch: “Laying out the control cabinets used to depend on the lead project engineer and electrical designer, meaning a different arrangement each time. For customers who regularly purchase switchgear systems from us, it could be quite annoying. Now with Cogineer, the motor safety switch or the circuit breaker, for example, is always in the same place.” Another advantage is the fact that it is quick and easy to add new functions to the tool for automatic schematic generation.
Engineering With Fewer Mistakes and Faster Onboarding
Moreover, as those responsible point out, using Cogineer leads to a reduced inventory because the same devices are selected for one and the same tasks. Errors occur less frequently because the functional modules are tried and tested. And when new employees are needed in the electrical engineering team, onboarding them goes much faster. Strusch: “They can really start working on one of our projects completely from scratch, without having to worry about how the schematics are supposed to look, and quickly get up to speed and work productively.”
“Installed” Engineering Knowledge
Right now, twelve of the eighteen electrical engineers at Siemens Leipzig are currently using the Cogineer configurator as their “project builder”. And there’s one designer in the team, Florian Pusch, who aside from being project director for automatic schematic creation is also developing new standard functions and implementing them in Cogineer. The electrical engineers have been asked for their suggestions. There are currently about fifty configurable functions with around one thousand devices stored in EPLAN Cogineer.
As Pusch says, the general goal when introducing Cogineer was to “install” as much knowledge from design and manufacturing as possible into the system or to depict it there: “My co-workers reported exactly how they created schematics, how a field is equipped and which functions could be combined with one another. This expert knowledge is stored in the software and is applied to every single project.”
Integrated Process Chain
Siemens in Leipzig also introduced EPLAN Pro Panel – for three-dimensional control cabinet design – at the same time as Cogineer. Tobias Isensee is responsible for the project. He sees clear advantages for introducing the two EPLAN modules in parallel: “The working methods in Cogineer, for instance setting connection definition points, meant that we were able to use Pro Panel productively in no time at all. Now we’re working with an integrated process chain for the electrical designs.”
As an example, this improves the (external) wire pre-processing. Isensee: “We have very special requirements here and use quite a lot of cross-sections and colours. These can easily be depicted in Pro Panel. And the automated wire routing increases the quality and ensures a uniform look within the control cabinets.”
Siemens has also defined standards for the mechanical components in Pro Panel. “The mounting panels are equipped with cable ducts and DIN rails as standard, which means that the electrical engineers can optimally place the devices according to in-house specifications that were developed in conjunction with the manufacturing department. This also improves quality.” For Siemens, the calculations of the cable duct fill capacity and collision checks are also very practical tools, not to mention that Pro Panel also simplifies the work involved in ordering devices such as terminals.
Saving Time and Money
The Siemens engineers naturally evaluate very carefully the relationship between the effort required and the savings, both in terms of costs and throughput times. Strusch: “At the moment the planning phase partly requires more effort. This is due to the higher degree of detail in the electrical engineering designs. We used to sometimes be a bit faster with the schematics. But now the Cogineer software is helping us with that, making up for any ‘lost’ time.”
The team reports that the workload for wiring has been significantly reduced: “Because the technicians receive fully labelled and assembled wires, we require up to forty per cent less time for wiring in some cases. The wires are a bit more expensive because they’re pre-processed, but the bottom line is that it saves us a lot of effort. Additional costs due to errors have also been reduced because of the quality improvements thanks to the automatic wire routing.”
Ongoing Self-Optimisation
Siemens views the introduction of Pro Panel and Cogineer, which began in 2018, as an ongoing process that is not yet complete in terms of continuous self-optimisation. Pusch: “We provide a new Cogineer release every month, which also incorporates feedback from engineering or modified device data. We then enter these changes centrally and have the advantage of not having to change or edit fifty macros.” The engineering department also benefits from this “installed” quality improvement: “If we receive information from production that a specification couldn’t be implemented, we adapt it directly in Cogineer.” Those responsible for the project are also in continuous contact with EPLAN: “Things that we ask for are often taken into account and introduced as part of new functions.”
Waiting for the Cloud Solution
The Siemens electrical design engineers in Leipzig are currently planning to implement the use of ePulse, the cloud-based platform for electrical engineering that enables collaboration and access to all projects. Strusch explains why this is interesting for them: “We work closely with other Siemens facilities in several countries, including Portugal, China and Turkey. As the lead factory, we often take over the planning and some of the engineering for systems manufactured in these various facilities. The standardisation via EPLAN has already helped us quite a bit in this. If we could now connect to these ‘hubs’ on a common design platform, this would be a further step towards standardisation and also open up new opportunities for collaboration across facilities. We’re really looking forward to it, especially since we’ve already been able to test the cloud version as part of a development cooperation with EPLAN.” They won’t have to wait long: the corresponding cloud software eBuild should be available to users in June 2020.
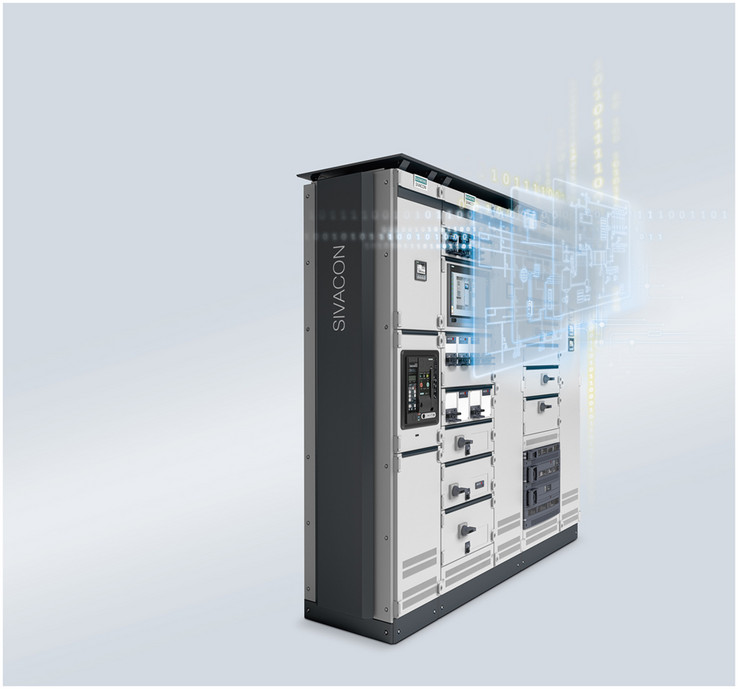
The SIVACON S8 low-voltage power distribution system and motor control centre from Siemens is used in many of the company’s international infrastructure projects.
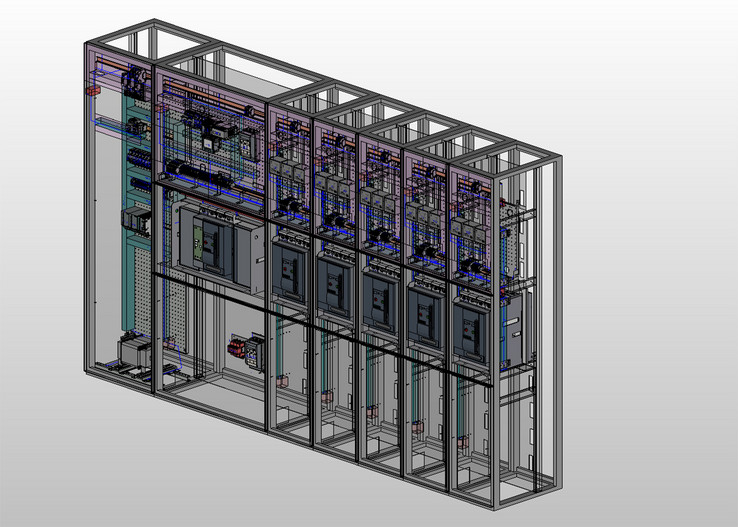
The Siemens electrical design engineers find that three-dimensional control cabinet designs with EPLAN Pro Panel offer numerous advantages.
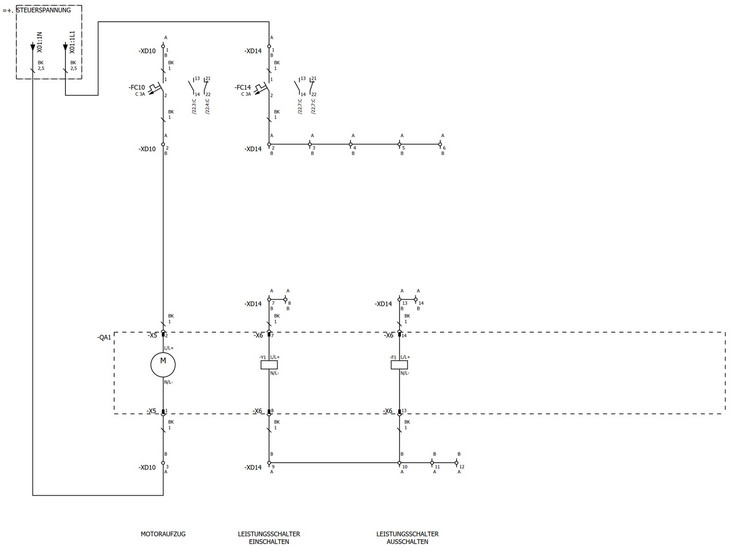
EPLAN Cogineer enables the electrical design engineers in the Siemens facility in Leipzig, Germany, to automatically create schematics.
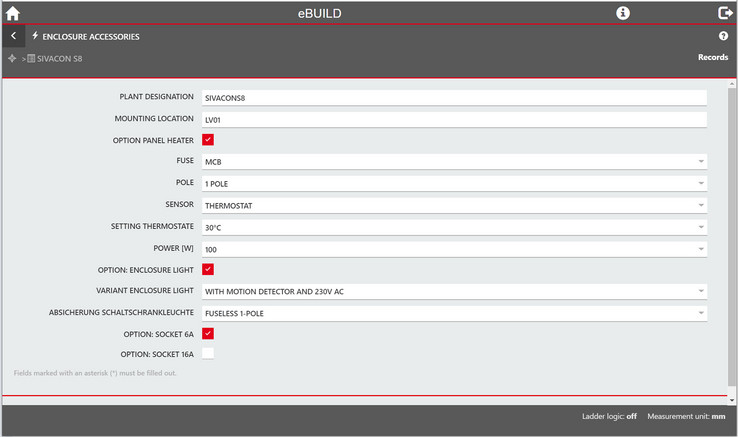
Configuring instead of constructing: the design methodology fundamentally changes with EPLAN Cogineer.
Photo credits: Siemens AG