Electric Powertrains for Mobile Machinery
SUNCAR is thus pioneering the electrification of motors for mobile machinery.
To decisively reduce carbon-dioxide emissions more vehicles will need to be built with zero-emission powertrains. However, this shouldn’t apply only to vehicles out on the roads. The start-up company SUNCAR is thus pioneering the electrification of motors for mobile machinery. To be able to respond quickly and efficiently to customer needs, the company uses EPLAN engineering tools.
SUNCAR was founded in 2015 by ETH Zurich, one of Switzerland’s leading science and technology universities. The company’s slogan, “Maximum performance – minimal emissions,” underscores its vision of advancing the energy transformation with the electrification of vehicles. Stefan Schneider, SUNCAR founder and general manager, has clear ideas about where his relatively new company is headed. With his Master of Science degree in mechanical engineering from ETH, he also knows the value of powerful software tools for day-to-day development work. That’s why SUNCAR uses EPLAN ECAD solutions for its electrical engineering.
The Desire: To Develop Something Groundbreaking for the Environment
“As a young, innovation-driven, 25-member team with well-educated employees, we feel the desire to implement ideas and inspirations, actualising ourselves in the process,” Schneider says. “We’re bringing together engineers who want to help shape and change the future of mobility.” With these two statements, he really sums up the spirit at SUNCAR: to create something that provides social benefits and massively reduces the burden on the environment.
Everything began back in 2011, with the development of electric powertrains for sportscars and traditional road vehicles. Starting in 2015, the newly founded company SUNCAR turned its sights to mobile machinery with a focus on the construction industry and municipal vehicles. “The advantage SUNCAR has is that we don’t have any cumbersome prior knowledge about the particular use of the machine in question,” Schneider explains. “We look at the application and then search for the best solution, regardless of its history. This produces innovative results that resonate with most customers. So far, we’ve received so much attention that customers are contacting us, so we haven’t had to focus on acquiring clients. We continue to develop as a company with every application we design. And we try to open up new markets with our established products.”
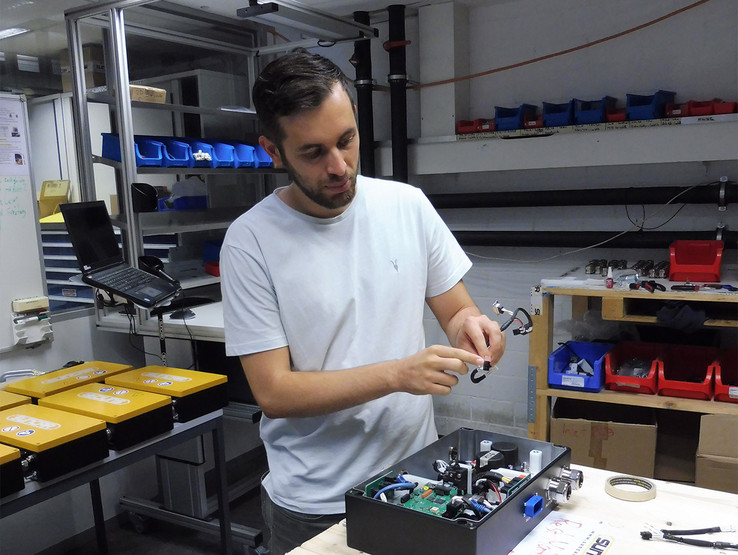
Stefan Schneider explains what is important for cabling connections on mobile machinery.
“Getting up to speed with EPLAN engineering tools goes very quickly. In two to three weeks, designers are working productively with them, which never ceases to amaze me.”
(Source: Lion Communication)

Careful designing of the electrical assemblies is elementary for Stefan Schneider.
“The idea of improving the world with our solutions is enormously motivating. Our focus is always on an energy-efficient vehicle.”
(Source: SUNCAR)
Electric Powertrain Solutions for Excavators
At the moment, SUNCAR develops the majority of its electrified powertrain systems for excavators. The first of these traditionally diesel-powered machines were electrified in collaboration with the Austrian investor Huppenkothen. The knowledge acquired from this work was subsequently used to install electric powertrains into more and larger excavators. “Until now, only the main powertrain and some auxiliary drives such as climate controls and fans have been electrified,” Schneider says. “We do have some ideas about how we could further increase a machine’s efficiency and, for instance, how we can make the hydraulic systems more efficient or even make them completely electric in some cases, but the costs for the latter aren’t commercially feasible at the moment. Hydraulics are well established in the construction industry and have proven their value. Next year we’re starting a research project with ETH Zurich to completely equip a two-tonne excavator to run on electricity and without hydraulics.”
Success with 3D Functionality
It’s clear that the complexity and flexibility of the projects require a sophisticated electrical engineering design tool. “SUNCAR started with just five of us and we didn’t have much experience,” Schneider recalls. “So, we asked some customers which ECAD they had had good experience with. That’s how we came across EPLAN. Since we didn’t have much liquidity, we liked the scalability of the licencing. On top of that, using the software is very intuitive. SUNCAR mainly employs younger engineers who have already worked with EPLAN design tools either during their studies or work experience, or who were able to quickly familiarise themselves with something new. As a result, introducing the tools went without a hitch and didn’t require much training.”
SUNCAR uses EPLAN Electric P8 for the electrical engineering as well as Harness proD, the tool for cabling and wire harness construction in 3D. “The intuitive 3D environment of the Harness proD tool in particular makes it much easier for us to design the wiring for excavators,” Schneider says. “It’s incredibly important for us to document the entire development process and do it in 3D. This is really in line with our basic approach to project work. Careful design and complete 3D documentation are simply part and parcel of our work at SUNCAR, something we also demonstrate to our clients. When we present the electrical schematics for the wiring, we also include how they are installed in the machine. This was initially met with a certain scepticism, especially from larger corporations, but this quickly dissipated for the most part. In the past, they had simply got used to doing this process themselves on a physical prototype.”
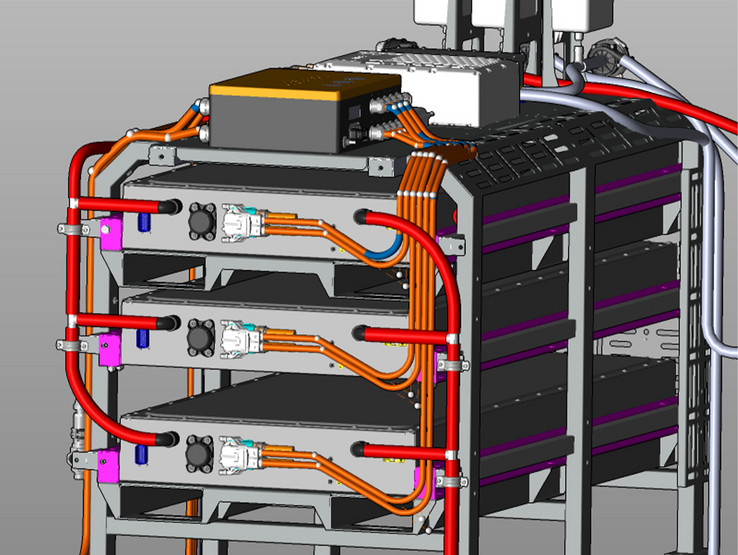
With EPLAN Harness proD, the digital twin of the cable routing can quickly be depicted in 3D.
(Source: SUNCAR)
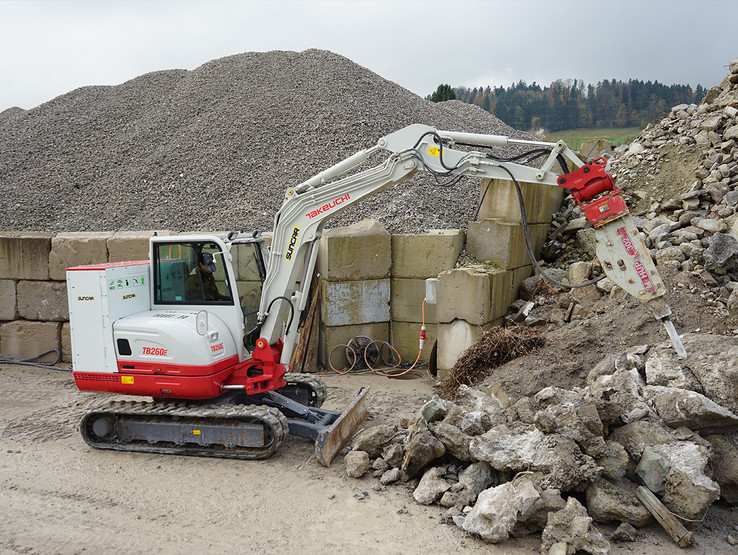
The SUNCAR TB260E excavator, weighing 6,780 kilos, in action.
(Source: SUNCAR)
Perfect Interplay Between Tools
Another major advantage of Harness proD is the possibility to import mechanical engineering data from 3D CAD tools such as SolidWorks. SUNCAR receives 3D construction data from customers, which means that the digital twin of the cabling can be very quickly displayed and optimised using Harness proD. The company then uses Electric P8 to design the logical connections for the control system and the electrical components and to position necessary shielding. For the actual arrangement in 3D space, designers are supported by Harness proD – they place the components and connectors in the vehicles and transfer the connection information from the schematics. In this way, the wire harnesses are routed and connected to the correct points. Thus the correct wire lengths are already determined during the design phase, which saves on materials in the end and enables precisely prefabricated wire harnesses. Once the routing has been completed, the system performs a validation check, detecting any trouble spots early on and warning the designer if, for instance there isn’t enough space at a certain point for the cabling. This helps reduce sources of error during the design phase.
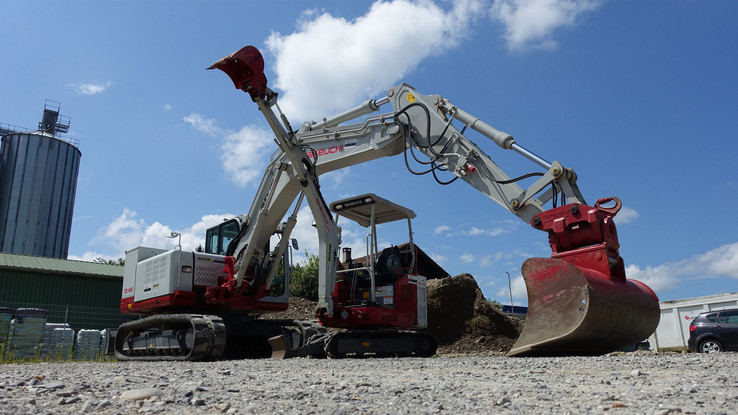
Intuitive and Easy to Use
Schneider’s experience so far has been positive: “What pleasantly surprises me is the fact that our engineers so quickly get up to speed using the EPLAN design tools. Right now, six engineers are using them regularly and we also employ interns from time to time. The interns usually start working productively after two to three weeks, which speaks to how intuitive the ECAD system is. The possibilities of the 3D digital twin, as well as the import of the vehicle’s CAD data with Harness proD, reduce our development times.” Another huge plus with Harness proD is the fact that designing with the tool has almost entirely eliminated mistakes and inconsistencies in cable routing. The complete data for manufacturing wire harnesses also simplifies collaboration with third-party suppliers. Versioning for the CAD designs is also planned for the future. “Versioning is also important for our clients,” Schneider adds. “This means they’ll always know the current status of revisions.”
What’s next for SUNCAR? Schneider: “After electrification comes automation for mobile vehicles and machines. We see a lot of potential there. Certain tasks can be made easier for the drivers or even taken over completely. We’re also focusing on further electrification applications; maritime and rail drives are also exciting challenges that we’d like to tackle. However, that’s all still a long way off.”
Author: Andreas Leu, Lion Communication